CLEAN ROOM: GUIDA AGLI STANDARD DA MANTENERE NEGLI AMBIENTI DI PRODUZIONE AD ARIA CONTROLLATA
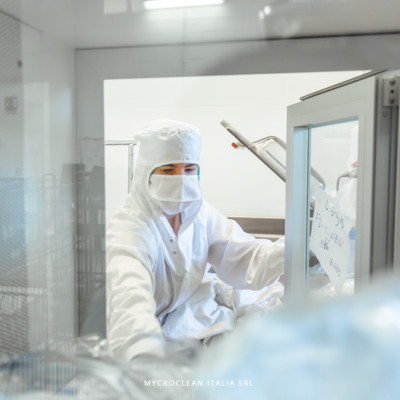
COS’È UNA CLEAN ROOM?
Esistono differenti modi di nominare questo tipo di ambienti, si potrà, perciò, sentir parlare di: clean room, camere bianche, ambienti ad aria controllata e camere sterili. Sono nomi diversi che vengono utilizzati per definire il medesimo tipo di ambiente, che ha, a prescindere dal nome con cui verrà nominato, degli standard fissi da mantenere.
Per definizione, una clean room è:
Una stanza in cui la concentrazione di particelle sospese nell'aria è controllata ed è costruita e utilizzata in modo da ridurre al minimo l'introduzione, la generazione e la ritenzione di particelle al suo interno e in cui altri parametri rilevanti, come temperatura, umidità e pressione sono controllate, se necessario.
Le clean room sono, perciò, ambienti controllati in cui i prodotti vengono fabbricati, assemblati ed imballati, ad un livello di contaminazione controllato che viene specificato dal numero di particelle, di una determinata dimensione, presenti per metro cubo.
IN QUALI SETTORI VENGONO UTILIZZATE LE CLEAN ROOM?
Le clean room vengono utilizzate in tutti i settori in cui le microparticelle possono influire negativamente sul processo di produzione dei differenti prodotti.
Esistono diverse classificazioni per questi ambienti, che sono stabilite in base alla pulizia dell’aria (e non solo) al loro interno e sono ampiamente utilizzate in vari settori: farmaceutico, biotecnologico, aerospaziale, militare e nella produzione di semiconduttori e dispositivi medici.
PARAMETRI DI CLASSIFICAZIONE DI UNA CLEAN ROOM
Per classificare una clean room bisogna tener conto di differenti parametri stabiliti dall’ultima normativa UNI EN 14644-1, applicabile in qualsiasi stato.
In base alla quantità di particelle presenti in un metro cubo all'interno della stanza è possibile suddividere lo standard di una clean room in nove classi di pulizia: partendo dalla classe di pulizia ISO 1 (10 particelle 0,1 µm, 2 particelle 0,2 µm), che è identificata come la più alta, fino ad arrivare alla classe di pulizia Iso 9 (35.200.000 particelle 0,5 µm, 8.320.000 particelle 1 µm, 293.000 particelle 5 µm), equivalente alla classe meno pulita.
Per dare un’idea di quello che viene misurato specifichiamo che: un micron (µm) equivale ad un centesimo della larghezza di un capello umano. La particella più piccola percepibile ad occhio nudo è larga 10 micron.
La classe di pulizia, come stabilito dalla normativa, viene definita anche in base alle misurazioni eseguite durante i tre stati di occupazione della camera:
At build: misure eseguite nell’impianto una volta completato ma ancora privo di macchinari e personale.
At rest: misure eseguite con i macchinari in funzione ma senza la presenza di personale.
In operation: misure eseguite con macchinari in funzione e normale presenza degli operatori.
FLUSSO DELL’ARIA ALL’INTERNO DI UNA CLEAN ROOM
Per mantenere “sterile” una clean room, ed ottenere così un ambiente privo di particolato (polvere, microbi e microorganismi), vengono utilizzati dei filtri HEPA (High Efficiency Particulate Air) o ULPA (Ultra Low Penetration Air), che utilizzano i princìpi di flusso d’aria laminare o turbolento.
Una corretta progettazione di una clean room comprende anche l’intero sistema di ventilazione e distribuzione dell’aria, designando la disposizione in modo da avere un adeguato ritorno dell’aria a valle. Negli ambienti a flusso verticale, significa avere un ritorno dell’aria nella parte bassa della parete lungo tutto il perimetro dell’area di lavorazione, mentre negli ambienti a flusso orizzontale si richiede l’uso dei ritorni d’aria lungo il confine a valle del processo di produzione.
Seguendo questi princìpi fondamentali l'aria esterna alla clean room viene fatta circolare all’interno del sistema di filtraggio dove viene decontaminata secondo le specifiche richieste, per poi essere immessa all'interno della stanza. Allo stesso modo l'aria contaminata all'interno della camera viene spinta fuori grazie all'immissione dell'aria decontaminata proveniente dall'esterno, obbligandola al passaggio nel medesimo sistema di filtraggio, dove verrà ripulita e rimessa in circolo.
ZONE E GRADI DI RISCHIO ALL’INTERNO DI UNA CLEAN ROOM
All’interno di una clean room esistono differenti zone, ognuna delle quali è classificata con differenti gradi di rischio per la produzione.
Per poter accedere in queste zone, che devono attenersi a particolari requisiti richiesti dalla normativa UNI EN 14644-1, bisogna necessariamente passare attraverso delle zone di transizione definite airlocks (camere di equilibrio). Queste aree servono ad impedire il passaggio di flussi d’aria diretti provenienti da aree differenti e sono suddivise in tre tipologie:
Cascade airlock: hanno una maggiore pressione da un lato della camera rispetto all’altro.
Bubble airlock: hanno una pressione interna più alta rispetto a quella esterna.
Sink airlock: hanno una pressione interna più bassa rispetto a quella esterna.
Una volta superate le airlocks si ha accesso alle vere e proprie clean room che, oltre ad essere classificate in base alla classe di pulizia ISO, sono anche differenziate per zone e gradi di produzione:
Grado A: sono le aree in cui vengono svolte le operazioni più rischiose durante la fase di produzione.
Grado B: sono tutte le aree immediatamente circostanti alle aree di grado A.
Gradi C e D: sono tutte quelle aree in cui si effettuano operazioni meno rischiose ed i prodotti non sono a diretto contatto con l’ambiente circostante.
PROCEDURE, PULIZIA E MANUTENZIONE ALL’INTERNO DI UNA CLEAN ROOM
I protocolli di pulizia e manutenzione stabiliti per le clean room sono la prima ed immediata linea di misure da mettere in atto per migliorare la pulizia generale e il controllo della contaminazione all’interno di questi ambienti. Avere tutte le migliori tecnologie di filtraggio a disposizione sarebbe totalmente inutile se gli operatori incaricati della produzione all’interno non osservassero le linee guida per un corretto accesso alla clean room.
Alcuni dei più comuni agenti contaminanti riscontrati all’interno delle clean room, come ad esempio: polveri, liquidi, batteri, funghi, cellule epiteliali e capelli, umidità, tracce di cosmetici e profumi, lanugine e fibre di capi d’abbigliamento, sono tutti riconducibili al personale addetto alla produzione all’interno della camera stessa.
Per questo motivo il personale che viene selezionato per lavorare all’interno delle clean room dev’essere sottoposto ad una rigida formazione, molto approfondita, sul tema della contaminazione particellare. Devono indossare indumenti speciali, appositamente progettati per intrappolare gli agenti contaminanti prodotti naturalmente dal corpo e, entrare nelle zone di produzione passando attraverso le airlocks.
A seconda della classificazione ISO o degli stessi gradi di rischio della zona in cui si andrà ad operare, l’abbigliamento sarà differente: potrebbe essere limitato all’uso di un semplice camice da laboratorio e retine per i capelli ,oppure essere più esteso, obbligando l’operatore all’uso di tute protettive a più strati con l’ausilio di autorespiratori.
Tutti questi accorgimenti sono stati studiati nei minimi particolari per la protezione dell'ambiente di lavoro ma, anche dell’operatore stesso.
Il rilascio di sostanze dal corpo dell’operatore o dagli stessi indumenti di protezione potrebbe degradare le prestazioni finali del prodotto e, viceversa, la composizione di alcuni prodotti potrebbe risultare nociva per la salute degli operatori.
Per garantire degli standard elevati è necessario che le aziende includano i dipendenti nel processo di mantenimento degli standard di qualità, tenendoli informati su tutte le procedure, sia positive che negative e sulle valutazioni igieniche; garantendo, a tutti gli operatori interessati, l'accesso a tutte le taglie e le forme di indumenti protettivi, in modo che siano completamente aderenti al corpo.
Inoltre, è necessario assicurarsi che gli operatori eseguano un’accurata pulizia della mani, lavandosi fino ai gomiti per almeno 30 secondi, prima di completare la vestizione all’interno degli appositi spazi. Tutte le sezioni di accesso alle zone di produzione (airlocks) devono essere pulite quanto le zone di produzione e, davanti ad ogni ingresso in cleanroom dev’essere posizionato un tappetino adesivo per eliminare la presenza di agenti contaminanti dalle suole delle scarpe o dalle ruote dei carrelli trasportatori. Ogni zona di produzione deve avere superfici lisce, impermeabili e ininterrotte, essere arredata con mobili e attrezzature appositamente studiate per evitare la dispersione di particelle contaminanti, con angoli arrotondati e semplici da pulire e pavimenti adesivi.
I principali indumenti protettivi indossati per operare all’interno di una clean room sono: camici da laboratorio, grembiuli, tute, mascherine per il viso, retine per capelli, copribarba, berretti, cappucci, maniche, guanti, stivali, scarpe e copriscarpe.
Il tipo di abbigliamento che verrà utilizzato sarà stabilito in base alle specifiche della clean room in oggetto e del prodotto che verrà lavorato al suo interno.
Stessa regola vale per lo smaltimento degli abiti una volta usciti dalla camera di produzione: le clean room di tipo ISO 1 smaltiscono gli indumenti utilizzati dopo ogni processo produttivo, mentre le clean room con classificazioni ISO più basse possono arrivare a cambiare gli indumenti solo un paio di volte alla settimana.
Di seguito riportiamo un esempio di una lista di controllo per la procedura di vestizione per l’ingresso in clean room:
Prima di entrare nella camera di vestizione, è consigliabile non fumare da almeno 20 o 30 minuti prima dell'ingresso.
Evitare l'uso di profumi e cosmetici.
Rimuovere completamente tutti gli effetti personali, come ad esempio gioielli ed orologi.
Fare almeno tre passi con ogni piede sul tappetino adesivo, rimuovendo lo strato di tappetino sporco se necessario.
Usare un detergente per spazzolare le scarpe.
Indossare copriscarpe.
Indossare retina per capelli da clean room.
Lavarsi approfonditamente le mani.
Indossare le fodere dei guanti da clean room.
Applicare, se necessario, copribarba.
Applicare una cappa da clean room appena lavata.
Indossare la mascherina.
Indossare la tuta toccando solo la parte pulita della panca da vestizione.
Indossare il cappuccio della tuta.
Indossare le scarpette da clean room.
Applicare soluzione alcolica all’esterno delle fodere dei guanti.
Indossare i guanti da clean room.
Applicare soluzione alcolica sui guanti.
Assicurarsi che guanti e stivaletti si sovrappongano alla tuta.
Pulire la panca per la vestizione con un panno sterile.
Utilizzare uno specchio per un ultimo autocontrollo delle procedure.
Di seguito riportiamo, invece, un esempio delle procedure di pulizia da attuare all’interno di un clean room:
Evitare l’introduzione e l’utilizzo di detergenti non specifici per l’uso all’interno di clean room.
Utilizzare l’acqua deionizzata per il lavaggio di tutte le superfici: panche, pareti, pavimenti, ecc.
Utilizzare solo panni che limitano la dispersione di particelle durante la pulizia.
Utilizzare un sistema di pulizie multi-secchio, con secchi senza saldature e controllo dell’acqua sporca e pulita designato.
Aspirazione a secco e lavaggio dei pavimenti giornaliero, prima dei turni di produzione, con acqua distillata.
Lavaggio settimanale dei pavimenti mediante l’utilizzo di un panno umido e detergente apposito per clean room, acqua distillata e aspirazione mediante aspirapolvere munito di filtro HEPA.
Lavaggio e aspirazione a secco delle pareti settimanale, mediante l’uso di un’apposita spugna da clean room e acqua deionizzata.
Lavaggio e aspirazione a secco dei soffitti settimanale, mediante l’uso di un’apposita spugna da clean room e acqua deionizzata.
Effettuare il sottovuoto dei soffitti quotidianamente.
Lavaggio e aspirazione a secco delle finestre quotidiano, mediante l’uso di salviette IPA al 70% prive di lanugine.
Tutti i processi di pulizia giornalieri possono essere effettuati durante i normali turni di produzione, ad eccezione dei pavimenti.
La pulizia di flaconi e attrezzature leggere avverrà dopo ogni utilizzo, mediante l’uso di una spugna apposita e acqua distillata e saranno successivamente asciugati con l'aspirapolvere.
Cambio di tappetini e pavimentazione adesiva a seconda della necessità.